Risk Based Inspection
Risk Base Inspection – современная методология оптимизации инспекций, которая позволяет расставить приоритеты инспекций и, как следствие, стратегически правильно сконцентрировать ресурсы при условии достижения безопасной и стабильной работы.
Наши инженеры подготовят квалифицированные оценки и процедуры для проведения целевых инспекции там и тогда, где и когда они необходимы. Мы обладаем передовой практикой, используем высококачественное инспекционное оборудование и применяем российское программное обеспечение RBICONCEPT®.
Management System
ISO 9001:2015
ID 9000012276
www.tuv.com
Анализ RBI (Risk Based Inspection)
Внедрение инспекций с учётом факторов риска (ИУФР) приносит существенную выгоду и позволяет компаниям:
- отслеживать реальное текущее техническое состояние оборудования;
- снизить количество ремонтов оборудования и запасных частей к ним;
- своевременно планировать закупку необходимого количества запасных частей;
- контролировать качество выполненных ремонтных работ;
- повысить надёжность оборудования, продлить межремонтный период и срок службы;
- повысить уровень безопасности на своём предприятии.
Оборудование промышленных предприятий, работающее под давлением, подпадает под правила и требования надзорных органов. В том числе требования по инспектированию технического состояния оборудования для выявления дефектов и оценки остаточного ресурса. Интервал между инспекциями и их объем регламентируется нормативными документами в зависимости от типа оборудования и состава среды.
Одним из вариантов оптимизации инспектирования является применение методологии, основанной на оценке рисков.
Высокая эффективность данного подхода достигается за счет перераспределения ресурсов на инспектирование оборудования. Такое перераспределение возможно после оценки последствий и вероятности разрушения оборудования. По уровню риска, который равен произведению последствий и вероятности, становится очевидно, на каком оборудовании следует увеличить интенсивность инспекций или снизить. Такой подход к планированию и проведению инспекций называется Инспекция с учётом факторов риска (ИУФР).
В ходе применения подхода ИУФР рассматриваются последствия нежелательного события на здоровье и безопасность персонала, окружающую среду и материальные потери предприятия. На основании оценки полученных рисков определяется межинспекционный интервал и объем инспектирования оборудования.
Статистика стран, где методология ИУФР уже широко используется, показывает, что её правильное использование позволяет спрогнозировать и избежать до 80% поломок оборудования, механизмы повреждений оборудования и формируя стратегию инспектирования оборудования и мониторинга ТС (см. рисунок 1):
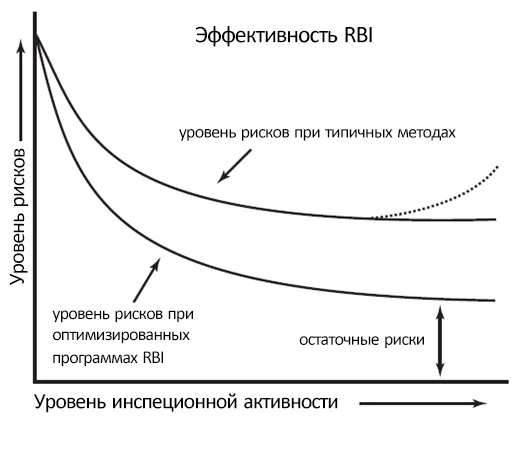
API 580, API 581, API 571
Для организации процесса RBI (ИУФР) в западных странах применяются следующие основополагающие нормативные документы:
- API-580 Risk-based Inspection;
- API-581 Risk-Based Inspection Technology;
- CWA 15740:2008 Risk-Based Inspection and Maintenance Procedures for European Industry (RIMAP);
- EN 16991 Risk-based inspection framework.
При проведении анализа на основе рисков (RBI) используется стандарт:
- API 571 Damage Mechanisms Affecting Fixed Equipment in the Refining Industry.
API-571 описывает механизмы повреждения оборудования в нефтеперерабатывающей и нефтехимической промышленности - является важным первым шагом в управлении безопасностью и надежностью оборудования, через идентификацию и понимание различных механизмов повреждения.
Ниже приведён сравнительный обзор ключевых стандартов, включая API, ГОСТ Р, CWA и EN, с указанием их роли в методологии RBI:
Обзор стандартов (API, ГОСТ Р, EN, CWA) по инспекции на основе рисков (RBI)
Стандарт \ Тип | Название | Отрасль использования | Связь с RBI | Краткое описание |
---|---|---|---|---|
API 510 \ Code | Pressure Vessel Inspection Code: In-Service Inspection, Rating, Repair, and Alteration / Код инспекции сосудов под давлением | Нефтегазовая, нефтехимическая, химическая, энергетика | Использует RBI для планирования инспекций сосудов | Инспекция, ремонт, модификация и переоценка сосудов под давлением в эксплуатации. RBI используется для оптимизации планов контроля. |
API 570 \ Code | Piping Inspection Code: In-service Inspection, Rating, Repair, and Alteration of Piping Systems / Код инспекции трубопроводов | Нефтегазовая, нефтехимическая, химическая, трубопроводы | Использует RBI для планирования инспекций трубопроводов | Инспекция, ремонт, модификация и переоценка трубопроводных систем в эксплуатации. RBI применяется для оптимизации контроля. |
API 571 \ RP | Damage Mechanisms Affecting Fixed Equipment in the Refining Industry / Механизмы повреждения оборудования | Нефтегазовая, нефтехимическая | Данные о мех. повреждениях для оценки вероятности отказа (PoF) в RBI | Описание механизмов повреждения оборудования. Основа для оценки вероятности отказа (PoF) в методологии RBI. |
API 573 \ RP | Inspection of Fired Boilers and Heaters / Инспекция печей и котлов | Нефтегазовая, нефтехимическая, энергетика | Может использовать RBI для планирования инспекций | Инспекция промышленных печей и котлов. RBI может использоваться для планирования инспекций этого оборудования. |
API 576 \ RP | Inspection of Pressure-relieving Devices / Инспекция предохранительных устройств | Нефтегазовая, нефтехимическая, химическая, энергетика | Может использовать RBI для определения интервалов инспекций ПУ | Инспекция предохранительных устройств (ПУ). RBI может помочь определить частоту проверок для управления риском. |
API 579-1/ASME FFS-1 \ Std / RP | Fitness-For-Service / Оценка пригодности к эксплуатации | Нефтегазовая, нефтехимическая, химическая, энергетика | Оценка пригодности (FFS) дефектов, выявленных инспекциями (в т.ч. по RBI) | Оценка пригодности к эксплуатации оборудования с дефектами. Анализ находок инспекций, часто планируемых с помощью RBI. |
API 580 \ RP | Risk-Based Inspection / Инспекция на основе рисков | Нефтегазовая, нефтехимическая, химическая, энергетика | Определяет основы и минимальные требования к методологии RBI | Основы методологии инспекции на основе рисков (RBI). Определяет минимальные требования к программе RBI. |
API 581 \ RP | Risk-Based Inspection Methodology / Методология RBI | Нефтегазовая, нефтехимическая, химическая, энергетика | Предоставляет количественную методологию для реализации RBI | Методология инспекции на основе рисков (RBI). Предоставляет количественные методы расчета риска для реализации API 580. |
API 584 \ RP | Integrity Operating Windows / Окна безопасной эксплуатации | Нефтегазовая, нефтехимическая, химическая | Данные (IOWs) для управления рисками в рамках программы целостности (включая RBI) | Окна безопасной эксплуатации (IOW). Определение критических параметров для контроля риска оборудования. |
API 653 \ Standard | Tank Inspection, Repair, Alteration, and Reconstruction / Инспекция резервуаров | Нефтегазовая, нефтехимическая, терминалы хранения | Использует RBI для планирования инспекций резервуаров | Инспекция, ремонт, модификация и реконструкция стальных резервуаров хранения. RBI помогает оптимизировать стратегию инспекций. |
ГОСТ Р 55234.3-2013 \ (Россия) ГОСТ Р | Инспекция на основе риска. Часть 3. Применение инспекции на основе риска | Нефтегазовая (особенно морские объекты) | Российский стандарт по применению методологии RBI | Устанавливает порядок и методические основы применения инспекции на основе риска для объектов нефтегазовой промышленности в РФ. |
CWA 15740:2008 \ CWA | Risk-Based Inspection and Maintenance Procedures for European Industry (RIMAP) / RBI и ТО для европейской промышленности | Энергетика, машиностроение, металлургия, химическая | Методология RIMAP, использующая RBI для планирования ТО и инспекций | Документ предварительного стандарта, описывающий единый подход к инспекции и обслуживанию на основе риска. Основа для EN 16991. |
EN 16991 \ EN | Risk-based inspection framework / Стандартизированная структура RBI | Универсальный (энергетика, химия, нефтегаз, переработка) | Европейский стандарт внедрения RBI-программы | Европейский стандарт по внедрению RBI. Обобщает и развивает подход RIMAP, формализуя структуру и требования к RBI-программе. |
Расшифровка терминов
- API (American Petroleum Institute): Американский институт нефти.
- ГОСТ Р: Государственный стандарт Российской Федерации.
- ASME (American Society of Mechanical Engineers): Американское общество инженеров-механиков.
- CWA (CEN Workshop Agreement): Документ, подготовленный в рамках рабочей группы CEN, не обязательный, но используемый как предварительный стандарт.
- EN (European Norm): Европейский стандарт, принятый CEN.
- Code (Кодекс): Документ, содержащий обязательные требования (правила).
- RP (Recommended Practice / Рекомендуемая практика): Документ, содержащий рекомендации и лучшие практики.
- Standard (Стандарт): Документ, устанавливающий нормы, правила, характеристики или методы.
- RBI (Risk-Based Inspection / Инспекция на основе рисков): Методология планирования инспекций, основанная на оценке вероятности и последствий отказа оборудования.
- PoF (Probability of Failure / Вероятность отказа): Один из двух ключевых компонентов риска в RBI.
- ПУ (Предохранительные Устройства): Оборудование для защиты систем от превышения давления.
- FFS (Fitness-For-Service / Оценка пригодности к эксплуатации): Оценка возможности безопасной эксплуатации оборудования с дефектами.
- IOW (Integrity Operating Windows / Окна безопасной эксплуатации): Установленные пределы параметров, влияющих на целостность оборудования.
- Мех. повреждения: Механизмы, вызывающие деградацию материала (коррозия, эрозия, усталость и т. д.).
Организация процесса RBI / ИУФР
Методология RBI позволяет построить эффективную стратегию технического обслуживания и ремонта статического оборудования, с учетом применения эффективных методов НК в необходимых объемах, в нужное время и в нужном месте для поддержания текущего уровня риска на приемлемом (допустимом) уровне.
Инспекции сами по себе не препятствуют проявлению механизмов деградации, но помогают в выявлении, определении характеристик, мониторинге и измерении данных механизмов деградации. RBI является бесценным инструментом предсказания типа и скорости деградации, что означает лучшую предсказуемость любого потенциального отказа. Инспекции способствуют уменьшению вероятности отказа и, следовательно, уменьшают риск. Схема менеджмента оборудования и место в ней процесса RBI выглядит так (см. рисунок 2):
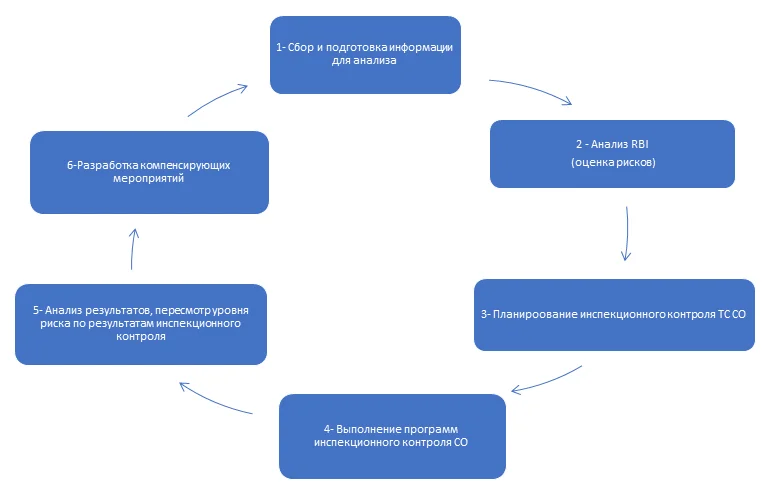
Организация экспертной группы
Для эффективного управления процессом RBI/ИУФР предприятия создают экспертные группы. В состав группы входят специалисты из смежных областей, обладающих достаточным уровнем компетентностей.
Примерный состав экспертной группы:
- Менеджер по надёжности оборудования – руководитель группы.
- Инженер по надёжности оборудования.
- Инженер по коррозии и материалам.
- Представитель департамента эксплуатации.
- Представитель департамента технического обслуживания.
- Представитель отдела ТБ.
- Другие специалисты по необходимости.
Определение механизмов деградации
Механизм деградации – это определенный вид воздействия на металл оборудования, возникающий при определенных условиях его эксплуатации, приводящий к потере несущих свойств металла и нарушению механической целостности (разгерметизации) оборудования. Потенциал воздействия механизма деградации (далее – МД) определяется на основании:
- состава технологической среды и агрессивности коррозионно-активных веществ в ее компонентном составе;
- рабочих параметров эксплуатации оборудования;
- материального исполнения оборудования;
- наличия и состояния защитных и изоляционных покрытий;
- наличия термической обработки элементов оборудования;
- воздействия климатических условий.
Определение контуров коррозии
Контур коррозии – участок технологической установки, который состоит из схожих конструкционных материалов и эксплуатируется в похожих условиях технологического процесса и, следовательно, подвергается аналогичным прогнозируемым МД, и имеет близкие по значению скорости коррозии. Одним из методов систематизации данных является создание контуров коррозии. Создание контуров коррозии – это систематизация оборудования с выделением в составе технологической схемы определенных схематических контуров, объединяющих технологически связанное оборудование.
Для каждого контура коррозии определяются критические параметры, которые оказывают влияние на деградацию оборудования, и которые должны контролироваться во время технологического процесса.
Оценка вероятности отказа
Посредством методики RBI определяются вероятности и возможные последствия отказов, на основе которых оценивается величина риска, и выстраивается соответствующая зависимость показателей анализа рисков от увеличения или снижения частоты ТО так, чтобы участкам, с высокой вероятностью риска было уделено особое внимание, в то время как участки с низким уровнем риска будут проверяться пропорционально своему уровню риска.
В рамках анализа RBI проводится оценка рисков и определяется вероятность потери механической целостности в зависимости от технических параметров и условий технологического процесса.
Оценка последствий отказа
Оценка последствий выполняется по итогам сбора и анализа таких данных как параметры основного режима, характеристика веществ, используемых в производстве, история отказов отдельных элементов оборудования и других.
Для каждого возможного режима отказа должны быть определены вероятность и последствия отказа. Последствия отказа могут быть разделены на три категории: экономические последствия, последствия для здоровья людей и ущерб окружающей среде. Все последствия выражаются в денежном выражении.
Общие последствия являются суммой перечисленных категорий последствий:
Общие последствия = Экономические п. + п. для здоровья людей + ущерб окружающей среде
Возможна классификация экономических последствий отказа оборудования корпоративной матрицей оценки рисков.
Степень последствий отказа или размера причиняемого ущерба ранжируются по 5-ти классам(Схема 3.5):
A – незначительные воздействие или ущерб;
B - малые воздействие или ущерб;
C -умеренные воздействие или ущерб;
D- Значительное воздействие или серьезный ущерб;
E – катастрофическое воздействие или масштабный ущерб.
Определение риска
Уровень риска определяется как произведение уровня вероятности отказа и уровня последствий отказа:
Стоит отметить, что вероятность отказа в данном уравнении является функцией времени. Это связанно с тем, что степень повреждения МД, от которой зависит вероятность отказа, увеличивается по мере накопления повреждений в компоненте со временем. Для удобства восприятия оценки рисков используют графический инструмент – матрицу рисков.
Матрица рисков
Ключевым элементом методологии ИУФР является матрица рисков. По одной оси отображается вероятность события, а по другой последствие события. Вид матрицы, категории последствий и вероятности могут быть изменены в зависимости от специфики предприятия, места его расположения, корпоративных, государственных и международных стандартов и правил.
Пример таблицы для ранжирования рисков (см. рисунок 3):
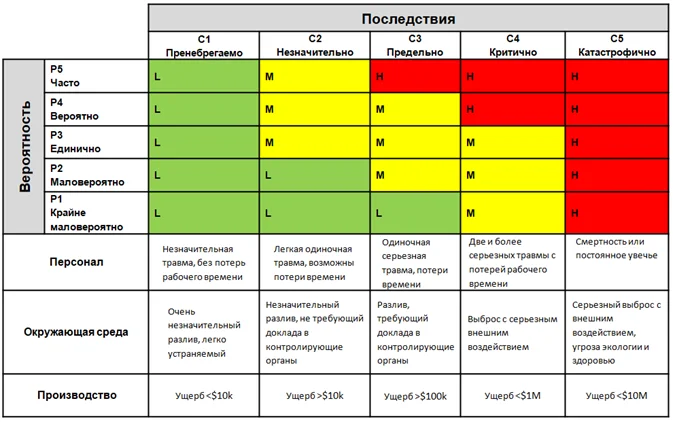
Определение этих параметров помогает установить уровень риска для каждой единицы оборудования или его элементов и установить интервалы инспекций на основе рассчитанного риска. Это позволяет исключить инспекции оборудования с низкими рисками, и сфокусировать усилия на оборудовании в критичной зоне рисков.
Процесс RBI / ИУФР с учетом вышеприведенного может быть отображен в виде схемы (см. рисунок 4):
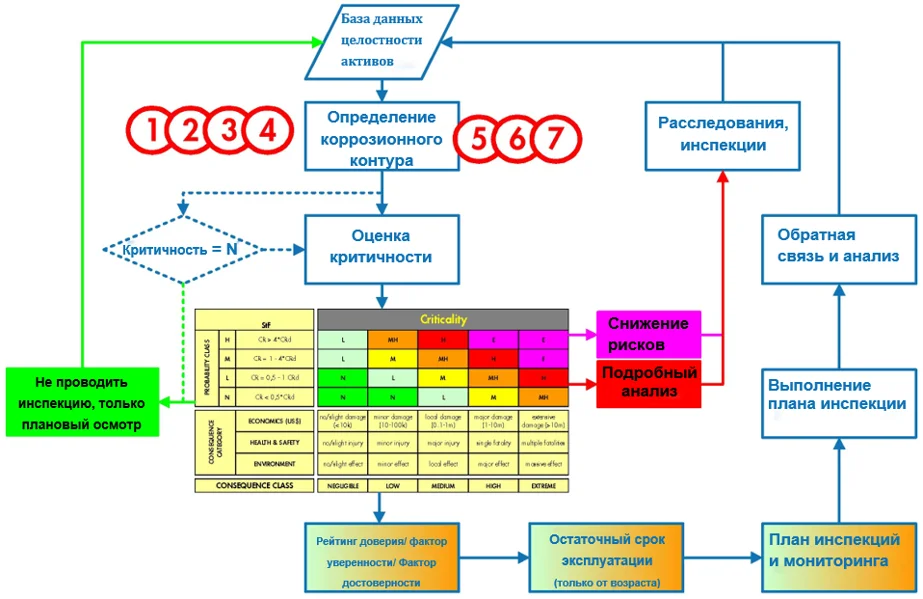
В ходе инспекции оборудования, риски, оказавшиеся в критичной зоне таблицы оценки рисков, требуют немедленных мероприятий по их снижению и переносу в жёлтую или зелёную зону. См. рис.4 Риски в жёлтой зоне, требуют оценки на предмет допустимости этих рисков, как приемлемые. Здесь используется принцип ПДНУ (практически допустимый нижний уровень), применение которого описано и нормировано в документе [7]. Руководствуясь этим принципом, экспертная группа ИУФР готовит рекомендации. Риски в зелёной зоне не требуют никаких корректирующих мероприятий. Возможно, требуется увеличение интервала инспекций.
Планирование контроля технического состояния оборудования
По результатам оценки риска, разрабатывается комплексная Программа проведения КТС СО, включающая в себя мониторинг технического состояния оборудования в процессе эксплуатации путем отслеживания показателей ООЦ, и инспекций.
Основой при планировании объема, выборе методов, сроков и периодичности проведения КТС СО, является результат оценки рисков по каждому оборудованию и должны быть соотнесен с Матрицей рисков.
Для каждого механизма повреждения, которому подвержен конкретный контур оборудования, вычисляется целевая дата проведения КТС СО. Целевая дата, это дата когда текущий риск достигнет максимальной величины приемлемого риска, это и является основным маркером для контроля и предупреждения возникновения отказа, поэтому установленные для оборудования объем и методы обследования необходимо проводить в сроки не позднее полученных целевых дат обследования.
Митигирующие мероприятия по снижению риска
В случае, если проведение инспекций не снижает уровень риска для оборудования, например, коррозионные дефекты приближаются к предельно допустимые отбраковочные величинами, либо интенсивность повреждений не позволяет вести дальнейшую безопасную эксплуатацию оборудования, могут быть выполнены следующие мероприятия, позволяющие снизить риск до приемлемого уровня:
- Изменение параметров технологического процесса;
- постоянного мониторинга параметров;
- Проведение ремонта оборудования;
- Замена элемента оборудования или всего оборудования;
- Проведение модернизации оборудования/установки;
- Применение дополнительных мер по защите от коррозии;
Определение и использование операционных окон целостности (ООЦ).
Для каждого анализируемого компонента оборудования или контура коррозии экспертная группа RBI определяет ключевые параметры технологического процесса или другие условия, которые оказывают влияние на скорость деградации.
Для каждого такого параметра устанавливаются границы оптимального, безопасного диапазона значений с точки зрения стойкости материалов. Диапазон изменения ключевого параметра в пределах установленных границ называют операционным окном целостности (ООЦ) (см. рисунок 4):
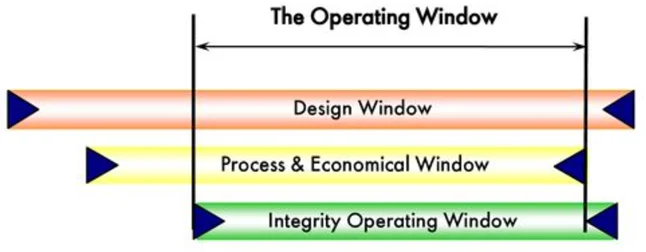
Возможности RBI
Внедрение анализа RBI/ИУФР позволяет:
- предотвращать отказы, инциденты и аварий за счет раннего выявления неблагоприятных изменений в состоянии оборудования;
- реализовывать меры по обеспечению надежности и безопасности оборудования в упреждающем порядке;
- выявлять механизмы разрушения, использовать методы контроля и митигирующие мероприятия в результате привлечения профильных экспертов;
- использовать наиболее эффективные методы НК за счет оценки эффективности инспекций;
- планировать техническое обслуживания оборудования с учетом его фактического состояния;
- обеспечить целостность за счет непрерывного улучшения процесса менеджмента оборудования;
- эффективно использовать ресурсы при менеджменте оборудование предприятия;
- создать систему менеджмента оборудования предприятия с понятными КПЭ, с возможностью планирования операционных и капитальных расходов.